During my WIL placement at the Herston Biofabrication Institute (HBI), I was given the opportunity to work on a cutting-edge project that aimed to develop the process of creating a 3D printed biocompatible prosthetic eye. This experience was invaluable for me as an Industrial Design student as I was able to use the design theories, CAD modelling, and project management techniques I had learned throughout my degree and apply it to a real-life project. As a biomedical designer intern, I was tasked with various responsibilities that helped me further my skills and knowledge in the field.
The need for and value of a 3D printed prosthetic eye is significant in the field of biomedical design and healthcare. The prosthetic eye is an essential component for individuals who have lost an eye due to injury or illness, as it helps to restore their appearance and self-esteem. With advancements in 3D printing technology, it is now possible to produce prosthetic eyes that are highly personalized, comfortable and biocompatible. By using a 3D printer, it is possible to create a prosthetic eye that is precisely tailored to the individual’s unique eye socket, providing a better fit and a more natural appearance. In addition, 3D printing also allows for a more efficient and cost-effective production process compared to traditional methods. With the increasing demand for advanced prosthetics, the development of a 3D printed prosthetic eye is of great value and importance, as it has the potential to positively impact the lives of many individuals.
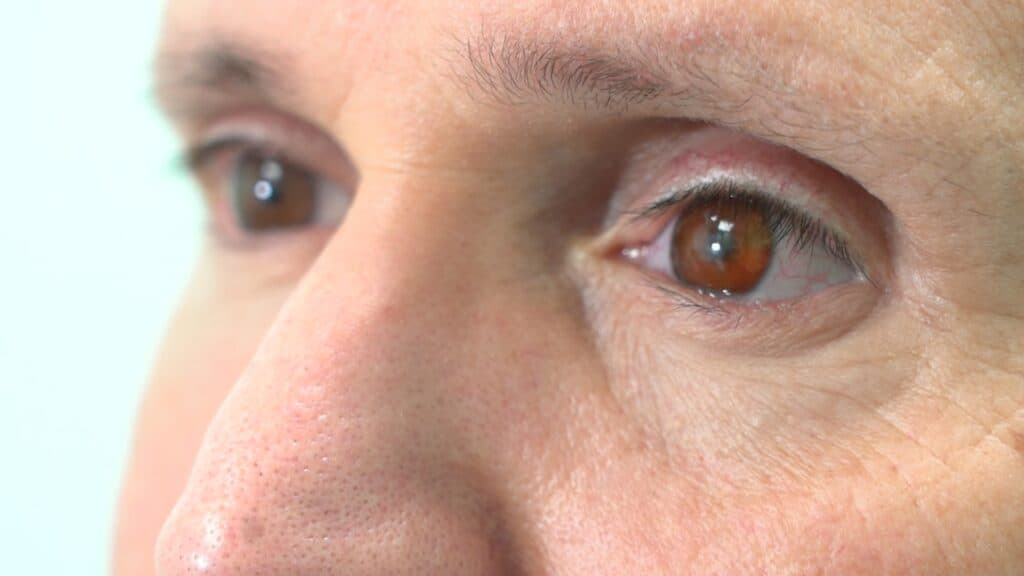
One of my key activities during my placement was conducting research and documentation of the project. This involved analysing and compiling information on different 3D modelling software that would be suitable for the project. I narrowed the selections to Rhino, Blender, and Houdini and presented a pros & cons comparison between them. It was decided that with my experience using Blender and the attributes identified in the software, that I was to focus my 3D modelling using Blender for the rest of the project. This also agreed with other scientific articles that were exploring the feasibility of 3D printing prosthetic eyes and had also used Blender for their 3D modelling.
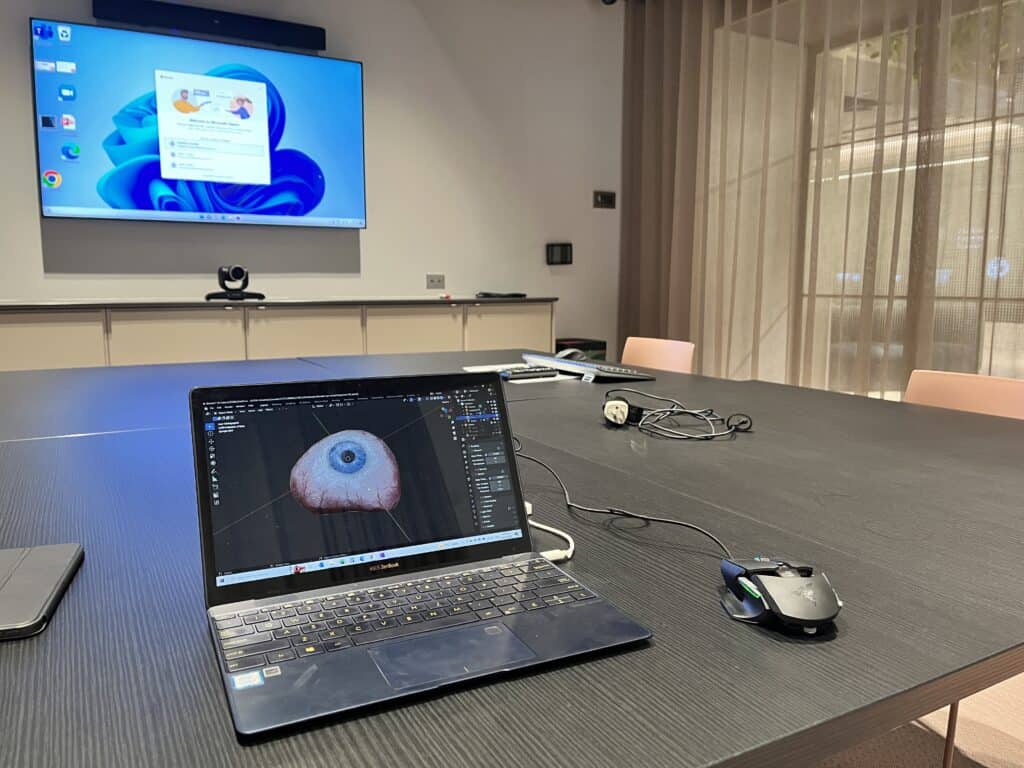
A highlight of my placement experience was the 3D modelling aspect. Using the software Blender, I was able to create various 3D models of a prosthetic eye with different design features. This allowed us to understand the potential solutions and improvements that could be made to the final 3D printed eye by comparing the different features present in each model. Unfortunately, these models were not able to be printed on the facilities Stratasys J750 3D printer as there is only a few times throughout the year where the printer was set to “colour mode” which is the mode needed to print my models. However, HBI has invited me to return and help them through the 3D printing and clean-up process once they determine a time that machine will be switched over to the correct mode. Regardless, this hands-on experience was incredibly valuable as it gave me a deeper understanding of how 3D printing technology can be applied in the medical industry.
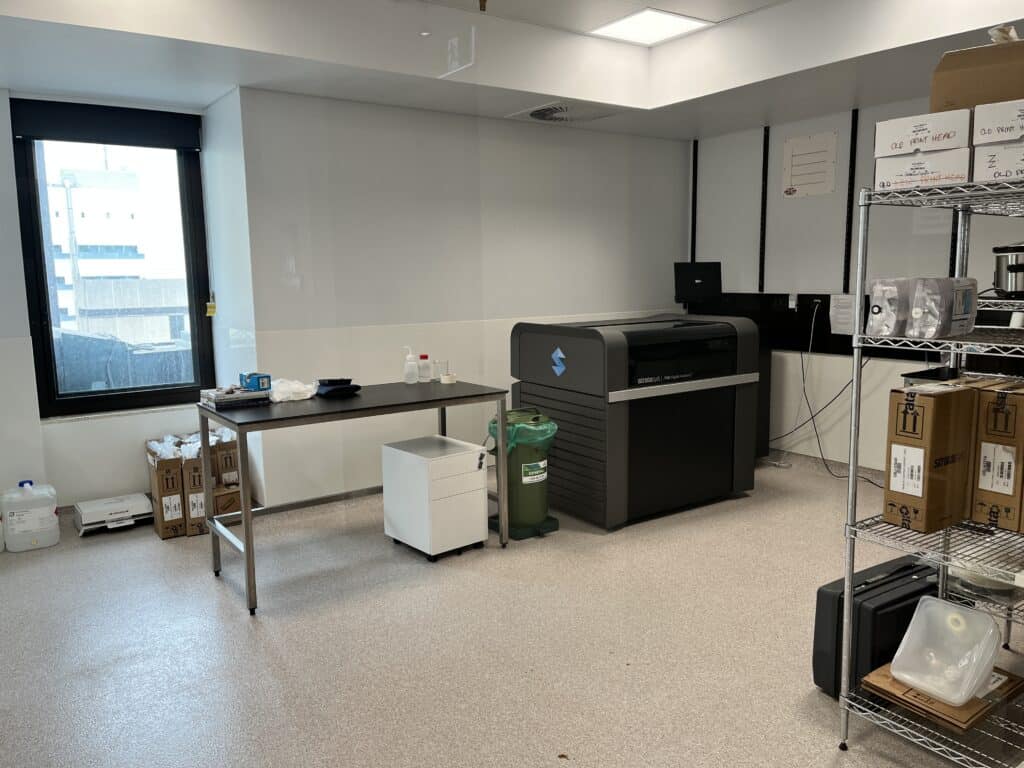
The deliverable of this project was primarily to produce a range of 3D models ready for 3D print with the various design changes between them, which would all have individual identification markings. These designs can then be assessed for the best qualities and potentially combined into a final model, which would potentially be used in the next stage of patient trials. This deliverable was important as it showcased the potential for using 3D printing technology to create biocompatible prosthetics in the future. This could have a real positive impact for patients who require prosthetics, as 3D printing technology offers a more personalized and efficient solution.
During my placement, I also developed several important skills and knowledge that will be valuable for my future career. These include problem-solving skills, technical knowledge in 3D printing technology, and teamwork. By working on this project, I was able to apply my problem-solving skills to find solutions to technical issues that arose during the printing process. Additionally, I was able to deepen my technical knowledge in 3D printing, which will be useful in future projects. Finally, by working in a team with different professionals from different backgrounds, I was able to develop my teamwork skills and understand the importance of communication and collaboration in the workplace.
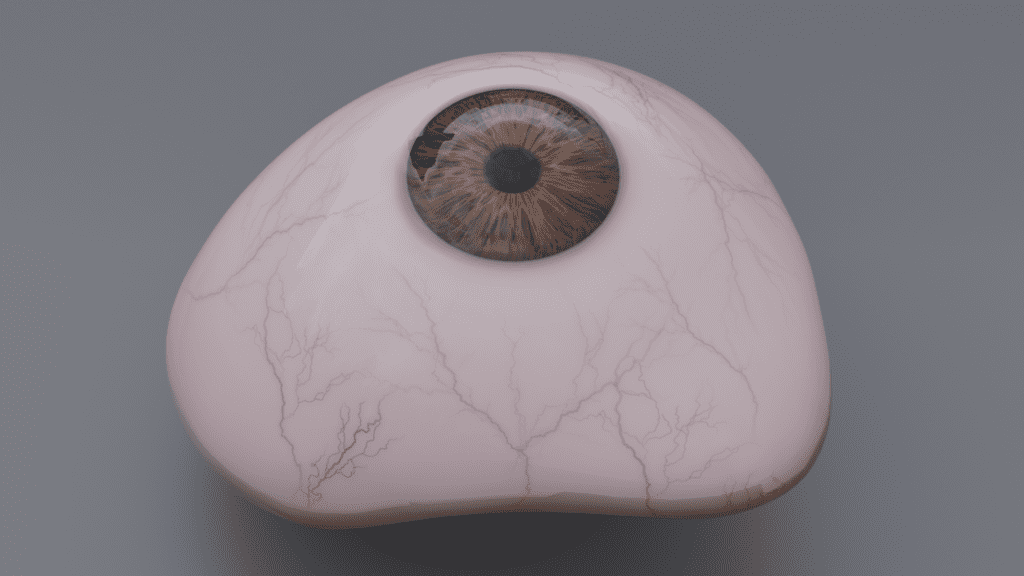
In conclusion, my WIL placement at HBI was a highly valuable and enriching experience. I was able to apply the scientific techniques, tools, and knowledge I had learned in the classroom to a real-life project. Additionally, I was able to develop several important skills and knowledge that will be valuable for my future career. Overall, this experience has solidified my desire to pursue a career in medical industry and has given me a deeper understanding of the potential of 3D printing technology.

References
cftassets.net 2023, World’s first 3D printed eye, Ctfassets.net, viewed 6 February 2023, <https://images.ctfassets.net/pjshm78m9jt4/57K5Axw9kDFfuXGNl0bqL/78deabb9f7d71c49748d67880a6689b1/3D_EYE_HL_IMAGE.jpg>.